QUALITY POLICY FOOD SAFE LIMITED
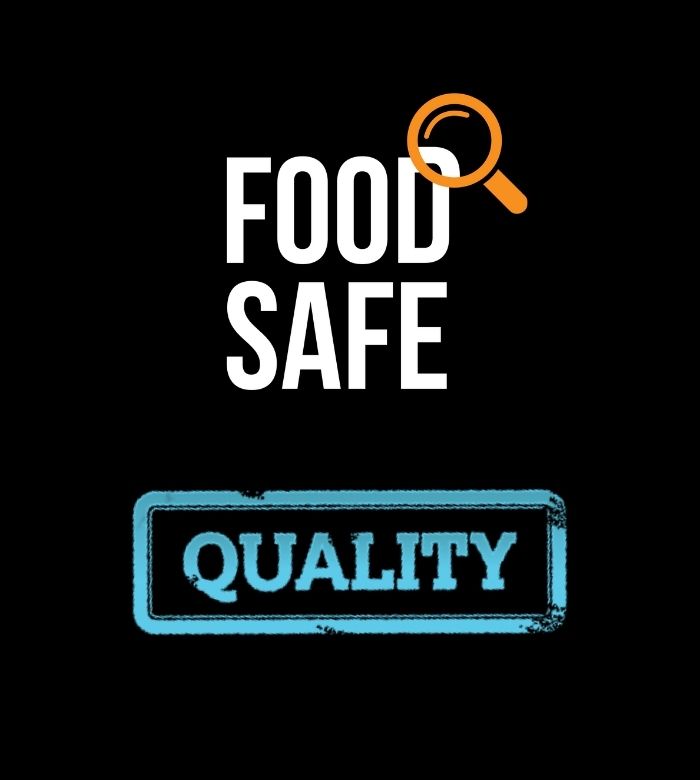
Food Safe Limited is committed to good professional practice and “Total Customer Satisfaction” through Quality in Development, Design, and Delivery for services in the area of Training and Inspection, Support, and Service.
Food Safe Limited’s management is committed to building on its market position and equity by providing total quality in customer satisfaction. Our mission is to supply our clients with on-time delivery of service, accurate and exact inspection results, which are of the best possible quality, are compliant with industry best practice, and consistently meet their design specifications and performance criteria.
In order to live up to our quality policy and objectives, our company shall service clients efficiently, economically, and on time with standards that consistently meet or exceed our clients’ requirements. This is accomplished through a continuing program to improve upon operational procedures and systems while striving to supply our clients with world-class service.
We shall endeavour to provide services that conform to the requirements specified by our clients under Quality Standards. Management’s responsibility is to provide direct leadership and resources to ensure continued conformance with these requirements. A cornerstone of our company’s Quality Policy is that excellence in services provided is the result of effort and commitment from all stakeholders. This commitment to quality shall be realized across all areas of the business.
The quality system is under regular review and audit. All stakeholders are invited to suggest possible improvements in working practice to the management.
Financial and partisan considerations do not influence Food Safe Limted’s service standards which have top management commitment to impartiality.
Food Safe Limited is committed to an exchange of experience with other inspection bodies and in standardization processes.
Objective evidence in support of our company’s Quality Policy is the responsibility of the Director.
KAUPAPA HERE KOUNGA
E pūmau ana a Food Safe Limited ki ngā mahi ngaio pai me te “Tino Āhua Reka o te Kiritaki” mā te Kounga o te Whakawhanaketanga, Te Hoahoa me te Whakarato i ngā ratonga mō te Whakangungu me te Tirotirohanga, Tautoko me te Ratonga.
E pūmau ana ngā kaiwhakahaere o Food Safe Limited ki te whakapakari i tōna tūranga mākete me te ōrite o te whakarato kounga whānui i roto i te āhua reka o te kiritaki. Ko tā mātau koromakinga he whakarato ki ā mātau kiritaki ngā hua ratonga, tōtika me te tirotiro tika, ki ngā kounga taumata teitei, he ū ki ngā mahi pai rawa o te rāngai, me te ū hoki ki ngā whakatakotoranga hoahoa me ngā paearu mahi.
Mō te eke ki ngā kaupapa here kounga me ngā whāinga, me tuku ratonga tā mātau kamupene ki ngā kiritaki kia māia, kia whai utu, ki te wā tika hoki ki ngā paerewa e ū ana, neke atu rānei ki ngā whakaritenga a ā mātau kiritaki. Ka tutuki tēnei mā tētahi kaupapa haere tonu hei whakapai ake i ngā hātepe me ngā pūnaha whakahaere me ngana tonu ki te whakarato ratonga taumata tiketike ki ā mātau kiritaki.
Ka whakapau kaha mātau ki te whakarato ratonga e hāngai ana ki ngā whakaritenga e tautuhia e ā mātau kiritaki i raro i Ngā Paerewa Kounga. Ko te kawenga a ngā kaiwhakahaere he whakararato ārahitanga tōtika me ngā rauemi hei whakarite ka whāia tonutia ēnei whakaritenga. Ko tētahi āhuatanga nui o te Kaupapa Here Kounga a te kamupene ko te tiketiketanga o ngā ratonga e whakaratohia ka hua i ngā mahi me te pūmau o ngā kaiwhaipānga mai katoa. Ka kitea tēnei pūmautanga ki te kounga puta noa i ngā wāhi katoa o te pakihi.
He auau te arotake me te tātari i te pūnaha kounga. Ka tonoa ngā kaiwhaipānga mai katoa ki te tuku whakaaro ki ngā kaiwhakahaere hei whakapai ake i te wāhi mahi.
Kāore ngā whakaaro pūtea, taituarā hoki e whai pānga mai ki ngā paerewa ratonga a Food Safe Limitied, ka pūmau ngā whakahaerenga tumuaki ki te tōkeketanga.
E pūmau ana a Food Safety Limited ki te whakawhiti wheako me ngā rōpū tirotiro, i roto i ngā tukanga whakakotahi hoki.
Nō te Tumuaki te kawenga taunakitanga tōkeke o tā mātau Kaupapa Here Kounga.

Keith Michael
Director – Food Safe Limited